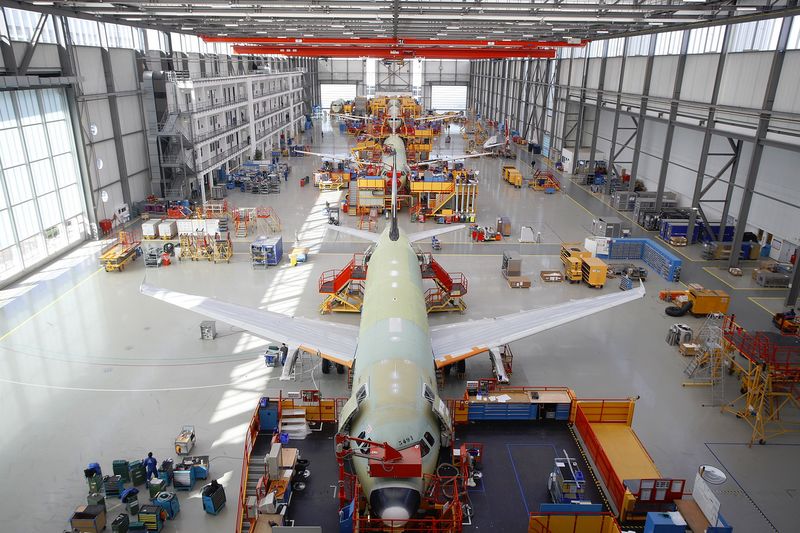
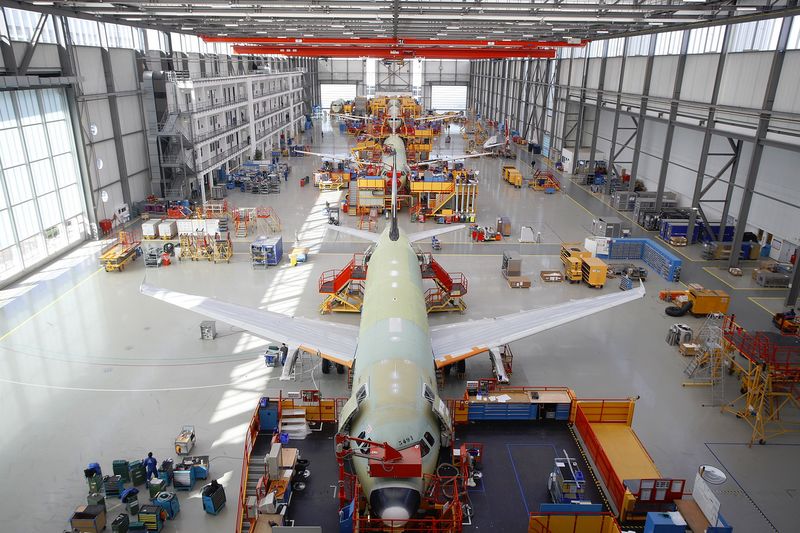
How Are Omnitrack Ball Units Used in Aircraft Assembly?
Omnitrack invented the heavy-duty range of ball transfer units in 1954. The patented “endless track” design allows heavy loads to be conveyed smoothly and precisely at any angle. The aircraft industry has relied on Omnitrack ball units ever since, enabling smooth aircraft assembly.
Ball units are used in the manufacturing processes and testing procedures of aircraft assembly — covering landing gears, fuselage, wing installation and many others. From their involvement in the production of the Comet in 1958 to the Eurofighter Typhoon in 1990 and — most recently — the Airbus Group and Boeing 787 Dreamliner in 2017, Omnitrack has been the first choice for ball units due to their consistently high performance.
Omnitrack Aircraft Industry Case Studies
Omnitrack 9241 ball transfer units featured in the production of the Eurofighter Typhoon in 1990. Eurofighter is the world’s most advanced swing-role combat aircraft offering agile performance, interoperability and unrivalled flexibility. Omnitrack ball units are an integral element of the aircraft’s design.
In 2009, Omitrack 9445 and 0454 ball units were used in the CERN “Hadron” collider particle research project. At CERN, the European Organisation for Nuclear Research, the world’s largest and most complex scientific equipment is used to investigate the fundamental structure of the universe. CERN chose Omnitrack ball units for their ability to perform to the highest standards under high temperatures.
Most recently, our 9840 units were used in the extensive testing of the landing gears in the new 787 Dreamliner. The designers needed to create a testing rig that could withstand the impact of 98 tons for over 100,000 cycles that they could reposition between tests. Unlike static tests — which push the aeroplane to extreme loads — the rig system allows for fatigue testing, which demonstrates the integrity of the landing gear in resisting the daily stresses. One can just imagine the challenging conditions our ball units face and overcome!
Managing Director of Omnitrack, John Cabrini-Dale said,
“I feel extremely proud that our units are a key part of the aircraft industry’s technological advancements and that we will always rise to the next challenge this industry presents, pushing our engineering forward.”
Why Are Omnitrack Ball Units the First Choice for Smooth Aircraft Assembly?
We asked John Cabrini-Dale why Omnitrack units play such a vital role in today’s aircraft assembly. He outlined four key reasons why the industry specifies Omnitrack units:
“First, is the highest load capacity possible – the largest of our units being able to support and move 4550 Kg [10,000 lbs] each.
Second, is the ability to use our units at any angle of orientation without any loss in load-bearing capacity or quality of movement, thanks to our patented “endless track” internal system.
The third is the “frictionless” movement our units can provide allowing heavy loads to be manoeuvred with supreme accuracy and minimal force.
Fourth is the high resistance to shock loads and extreme temperatures, allowing the units to be used in arduous conditions that traditional ‘hemispherical cup’ ball units would suffer in.
In the case of the Airbus project, our 9352 Omnitrack Ball Units are used in the final, delicate positioning of the wing’s terminal pins & fittings as they are inserted into large castings attached to structures on the fuselage. This allows the wings to be attached to the sub-section by thousands of bolts which, thanks to the precise movement of our ball units, can be aligned perfectly which is vital for the rapid & therefore cost-effective assembly of the aircraft.”
The Key to Smooth Aircraft Assembly
Omnitrack will remain at the forefront of the omnidirectional movement industry as we continuously strive to find new solutions for our clients. Our products have evolved over 100 years and we are always excited to work on custom designs to meet specific needs. We are proud of our reputation in the aircraft industry. Omnitrack ball units are the first choice for smooth aircraft assembly processes due to their high load capacity, “frictionless” movement, high resistance to shock loads and high temperatures, and the ability to use our units at any angle of orientation without any loss in load-bearing capacity or quality of movement.
We look forward to our next aircraft assembly product and the challenges it presents!